What is vulcanisation of rubber?
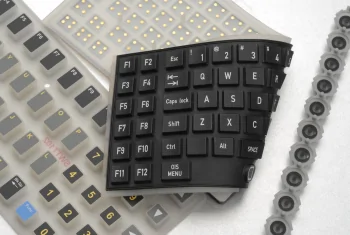
Vulcanisation is a process first discovered by Charles Goodyear in 1839 after mixing rubber and sulphur together on a stove, surprised that the mixture didn’t melt he increased the temperature and the mixture hardened.
Vulcanisation is a process first discovered by Charles Goodyear in 1839 after mixing rubber and sulphur together on a stove, surprised that the mixture didn’t melt he increased the temperature and the mixture hardened. He patented the process and named it after Vulcan, the Roman God of fire!
This discovery would change how rubber would be used forever.
Vulcanisation was discovered by accident, but we now understand that it is the cross linking of polymer chains to change a viscous polymer into a solid material. In the unvulcanised state, the polymer consists of long chains which can under stress slide over each other and so be useless as a solid rubber. Once vulcanised the chains of the polymer are joined to each other at the contact points.
Different rubbers use different chemistry to achieve these joints. With a silicone rubber, a variety of peroxide is the preferred material to make the crosslinks. Silicone rubber can also be crosslinked with a platinum catalyst. Using this system, the time of curing in a press can be reduced. Of course, different cure chemistries have different positives and negative effects, and it is up to the compound chemist to choose a system that is best suited to the process of production and the final product.
The vulcanisation process or “cure” takes place under heat and pressure to initiate the process. Some processes do use cold curing or “room temperature vulcanisation”, RTV. This process is used in the rapid prototyping of silicone mouldings. The pourable silicone is formed in a mould at room temperature. The disadvantages of this are that the cure takes a long time and the resultant product does not attain the same physical properties as an HTV silicone. Consequently, the product is more expensive to produce and not suitable as a mass production method.
Pre-vulcanised rubber comes in various forms, solid HTV (high temperature vulcanising), Liquid Silicone Rubber LSR, and various grades of RTV. For our purposes, we are concerned with solid HTV silicone rubber.
Silicone rubbers consist of long-chain polysiloxanes and various fillers, like pyrogenic silica. Vulcanisation changes them into silicone elastomers.
HTV Silicone rubbers are suitable for a wide range of applications, including electrical & electronics, mechanical engineering, food, health care and medical and automotive sectors.
Silicone rubbers have no known physical harmful effects, and they have excellent UV and ageing resistance. Silicone rubbers also exhibit a wide operating temperature range of -50 to +200°C (or greater for special grades).
We welcome customer visits to our factory, we can show examples of mouldings in silicone and other materials. Our silicone mouldings range from keypads with carbon contacts, seals and gaskets to metal bonded over-mouldings. We also make mouldings using other synthetic rubber materials like FKM, EPDM, Nitrile where certain physical or chemical properties are required.
If you have details of your requirement, please send these to us and we can help advise on material and of course offer a quotation.