Producing laser etched legends on keypads
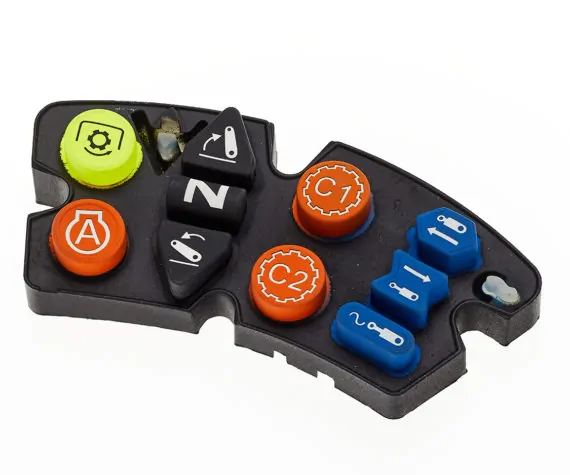
Laser etching is a process used to create backlit legends on silicone rubber keypads, where only the legends are visible when light is transmitted from below the keypad.
There are several operations involved during the production of laser etched keypads that are key to achieving the best quality finish.
After moulding the keypads need to be sprayed with a base layer of white silicone ink, this layer provides the legend colour so the legend is visible in normal light conditions and also when backlit will create a crisp clear, illuminated legend. It is critical that the white spray layers use correctly mixed spraying ink offering the best viscosity to provide a fine blemish free spray coating. If mixed incorrectly you can easily end up with an unpleasant “blotchy” finish to the keypad legend
The secondary coating is usually a black ink, again it is important that this layer also is mixed correctly as any surface defects or contamination in the ink or the spraying environment will be highlighted when the final product is illuminated.
For both the white and black spray coating operations consistency of thickness is extremely important, if uneven coatings are applied then the laser will not burn through the layers of ink cleanly so will offer a varied backlighting effect with the keypads are illuminated.
It is recommended that after each spray coating you inspect each part in a dark room on a light box to ensure maximum quality. This then allows the opportunity to increase the number of coatings applied in order to ensure no light leakage through the black coating before you laser etch. This inspection level will vary depending on the customer quality requirements.
Once the keypads have been sprayed in all required colours they are ready to be laser etched. Laser etching requires a positional jig for the part to ensure correct position can be retained during production. Once the jig has been set to the correct position then the laser settings need to be programmed, this involved several settings that will vary between machines. However speed, frequency and power are critical as well as ensuring the part is positioned the correct distance from the laser itself.
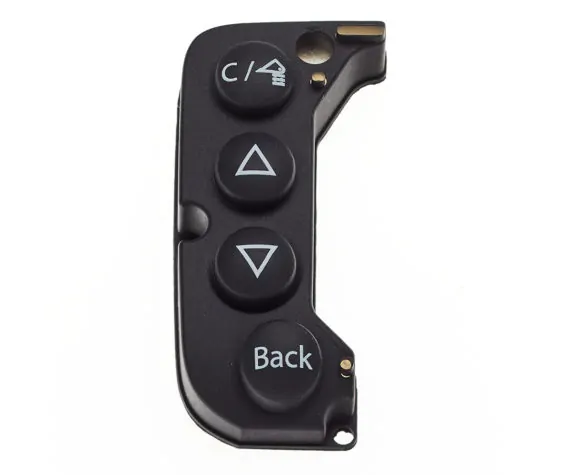
After etching parts should be checked on a light box to ensure the burn has been successful and that the backlit legends have no contaminants or remaining ink on the surface, often the parts may need to be wiped with isopropyl to clear any burn marks or excess ink residue off.
To ensure the spray inks do not wear over time it is usual to apply a clear protective coating to the moulding, this is often determined by the customer as each coating offers a slightly different surface finish. Silicone coating can offer a matt silky finish, PU coatings offer a smooth hard finish and for extreme protection you can apply a Parylene coating.
These processes are critical to producing quality etched keypads and inspection should be carried out after each of these operations as once the laser etching process is carried out the parts cannot be corrected.