Plastic and rubber mouldings in manufacturing
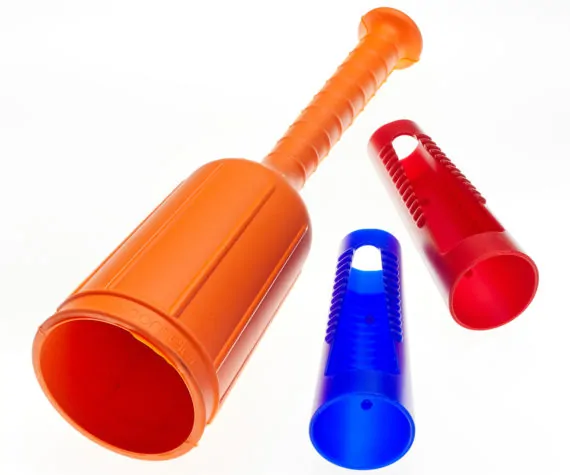
Before making the decision on what plastic or rubber moulding technique to choose and what will work for your product, it is good to see some of the options.
What material, or materials, do you need your finished item to be constructed from?
What shape do you require, to what tolerances, and for what purpose?
How many items will you need moulded options, and do you have a target unit cost?
This article summarises the various methods, their functionality and purpose.
What is Moulding
Moulding in simple terms is the shaping of either a liquid or moveable material using a mould. The process dates from the 1800’s and has evolved through time to become one of the most recognised methods of producing shaped components.
Types of Moulding
Injection Moulding
The process of injecting molten plastic or rubber into a mould at high pressure. Injection moulding is commonly used for bottle caps, medical devices, bumpers and electrical switches due to its flexibility. Very fine tool join lines are possible with injection moulding. Where rubber moulding is concerned, Liquid Silicone Rubber (LSR) is typically injection moulded. Multi-cavity injection mould tools are typical for higher quantities.
Compression Moulding
Uncured rubber is placed into a mould, the mould is closed and the material is compressed into the desired shape. A heating and curing process ensures the finished component is durable and strong. Compression moulding tooling is a relatively low cost which can offer clients savings. Multi-cavity tooling is usually used for higher quantities.
Transfer Moulding
A hybrid moulding method that fits between compression and injection moulding. Uncured rubber is put into a cavity in a mould tool, during the moulding cycle this cavity is compressed and the rubber is injected through passageways into the mould tool, to then take the desired shape and be cured. Multiple cavities can be used with transfer mould tools where volumes demand it.
Extrusion Moulding
With extrusions, a long shape is produced. Extrusions are made by squeezing a hot raw material through a custom die. Products such as hose pipes, gutters and pipes/tubes where a long mould is needed are all created using extrusion moulding, as are many rubber seals and UPVC window fittings.
Blow Moulding
The method of creating a hollow plastic part. It is mainly used on products where shape and thickness are essential. For those aware of glass blowing, blow moulding is the same principle. This option is used for bottles, drums, tanks and watering cans due to their hollow nature.
Rotational Moulding
The production of a large hollow part by inserting a powder or liquid resin into a mould and then rotating it. Also called rotomoulding. This is a popular choice for companies who require big orders for large parts. Rotational moulding is used for Recycle bins, kayaks and large car parts to name but a few.
Thermoforming
A plastic sheet is heated to a pliable temperature and formed to a specific shape in a mould. This is a cost-effective method due to the low-cost material used. It is commonly used for moulding plastic cups, lids and the lining of fridges. The food and retail industries rely heavily on thermoforming due to the requirement of mass producing items to support their products.
To discuss your own requirement with us, please make contact with our sales team who will be pleased to discuss your options in more detail.