Prototyping
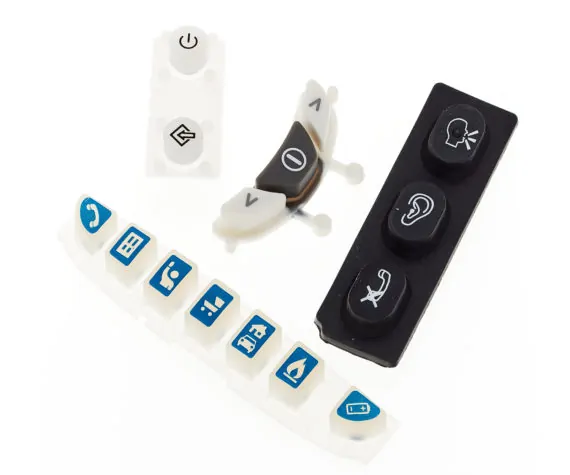
When starting out with a new design, prototypes will often be made.
Prototypes will often be made with methods that vary from planned production methods, to allow for iterations of design and to keep costs down.
The closer the prototypes are to the final production item, in terms of materials, dimensions and finish, the greater proof they can provide that the design is satisfactory to proceed onward to production. Timescales can be days rather than many weeks to make production fit tooling .
Methods for producing prototypes include:
3d printing the prototype:
Also known as Additive Manufacturing (AM), 3d printing can produce a part in “rubber like” materials. An advantage is that no mould tool needs to be made. The parts being in rubber like materials rather than actual rubber can be an issue because they won’t have the same physical properties as the rubber used for production.
3d printing a mould and moulding the prototype:
Print a mould then using this mould inject with liquid silicone rubber. This material has excellent engineering properties and the resultant moulding will represent closely what would be expected from production. There is one caveat that the surface finish will not be as smooth as say a machined tool.
An aluminium mould tool:
Using aluminium rather than tool steel is more economic in tool cutting time whilst maintaining surface and dimensional accuracy. The tool will be quite suitable for repeat sampling and is suitable for trialling all high consistency polymers. This is important if there is uncertainty on what polymer or hardness to use in multi cavity production.
Cutting a single impression into a steel tool:
Another approach is to cut just one cavity of the multi cavity tool and then sample. This can save time to obtain samples, also it makes it possible to alter some dimensions with the experience from the previous single cavity cut.
RTV Moulding:
Room temperature vulcanization (RTV) moulding is sometimes used for prototyping. A master item must be created and then a mould formed around it. Moulding can be done in PU or Silicone. A disadvantage is that RTV silicone does not have the same properties as HTV silicone in which the production items would be produced.