Rubber seals in electronic assemblies
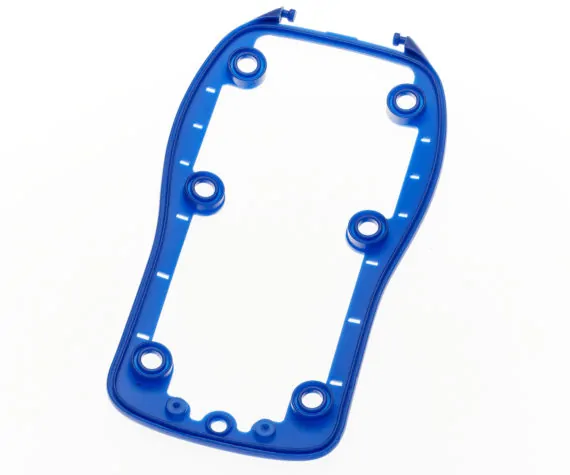
Rubber Seals are often an integral part of an electronic assembly. Seals, whether silicone or rubber, are required to protect the end product from environmental conditions that it is exposed to during use.
Rubber Seals are often an integral part of an electronic assembly. Seals, whether silicone or rubber, are required to protect the end product from environmental conditions that it is exposed to during use.
Rubber Seals can be designed to achieve what is called an International Protection Rating. This rating is an industry standard to classify the degree of protection against solid objects, dust and water. For example:-
For dripping water the specification would need to be IP61
For protection against water when the product is at a 15 degree angle the specification would be IP62
To protect against sprayed water up to 60 degrees from vertical the specification would be IP63
To guard against splashed water from all angles you would specify IP64
Protects against water jets you would specify IP65
For protection when immersed in water for a defined time, depth <1m and pressure then you would specify IP66
There are many materials that can be used to manufacture rubber seals; therefore it is important to make clear the envisaged environment when requesting a quotation. One should consider; temperature extremes possible, any chemical or solvent contact, bio-compatibility, electrical and RF requirements, exposure to sun and UV.
When designing rubber gaskets, remember that the rubber does not squash on compression and reduce in volume, it merely deforms. This means that if you have a seal situation with a large area to seal against, it could require a high compression to get both faces to securely mate together. There are ways to deal with this problem, which can be overcome.
Rubber seals can be produced by extrusion methods, punched from sheet if the profile is flat, moulded by compression or injection methods. All of these methods require tooling and this can range from low cost for punch tools to higher costs for the moulding compression or injection tools. The best method is ultimately decided by the design of the part and the estimated quantities required.
When designing the rubber seals, be aware that by making the profile too complicated this will not only effect the part cost but also effect largely the tooling costs, extravagant undercuts will mean a complicated tool design so try and keep these to a minimum. Ask your manufacturer for advice on solving your design issues, an experienced manufacturer should be able to advise what features are adding to the cost and suggest alternatives that may not previously been considered.